Follow these Blower Maintenance practices to prolong blower system life. Maintaining your blower properly now saves you money and increases your system uptime.
Featured Pump Articles
- Grundfos Pumps in Process Liquids Transfer
- Grundfos Pumps For Industrial Machining
- Turkey Processing Plant Saves $50,000 and Reduces Energy by 50% with a High Pressure Washdown
- Save up to 50% Energy by Optimizing Pumps
- Grundfos Food & Beverage Process Water Case Studies and Product Features
- AODD Pumps and Diaphragms for Food & Beverage Applications
- Are You Using Counterfeit Pirated AODD Pump Parts ?
-
Industrial Blower Service Maintenance Guide
- Wilden AODD Pumps Outperform ARO, Yamada, Graco, Sandpiper, Versamatic and Murzan
- Centrifugal Pump Training in Minutes by Griswold
- Market Proven! Ethanol Extraction Pumps
- Carotek solves customer's leaky seal and pump cavitation problem
- Gear Pump Troubleshooting Checklist and Videos
- Case Study: Plant Solved Shaft Breaks in Positive Displacement Gear Pumps?
- Request a FREE Pump Site Survey ($2500 value)
- How To Set Up a Pump Reliability Program - Do You Know When Your Pumps Will Fail Next?
- Tips to Improve Your Pump Uptime
Industrial Blower Service Maintenance Guide
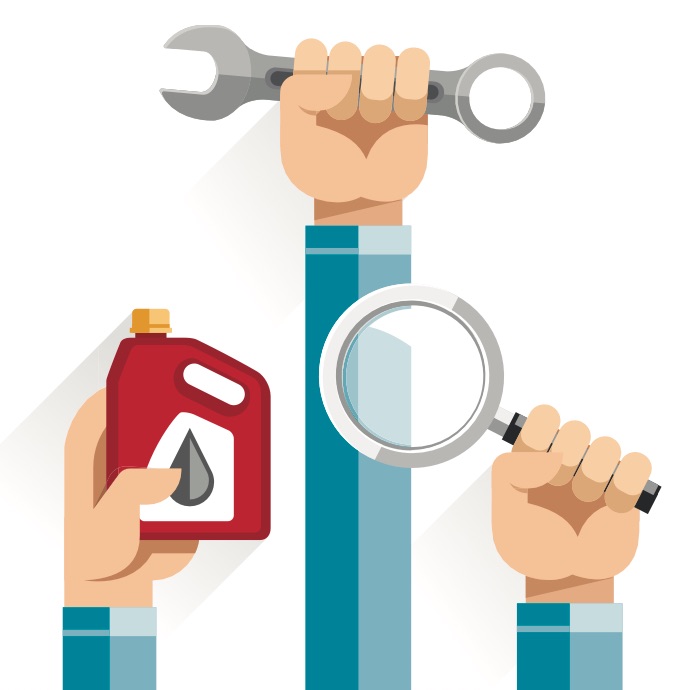
Blower Service, Inspections, Lubrication, Silencers & Vibration Monitoring
Consider a Service Agreement—If maintenance time and personnel are lean, outsource blower maintenance to a factory authorized distributor. The money spent here will pay for itself in reduced downtime, lower repair costs and electrical cost of operation savings. Top flight distributors have factory-trained technicians that will handle the basics while identifying significant savings opportunities in the system.
Periodic Inspections—A well-organized maintenance program will provide for periodic inspection of the blower, drive and components. These inspections may prevent major repair and downtime. Observe the blower for vibration, heating, noise, oil seal leaks, and excessive shaft air leaks. Check for proper operation of the filters, coupling, drive, power unit, relief and check valves, gauges and other controls. Disconnect the drive and turn the blower by hand to check for drag, tight spots, bearing wear (radial and axial) and gear backlash. Rotation should be free with no indication of drag or metallic interference. Inspect the interior through the inlet or discharge port for cleanliness, corrosion or parts contact.
Lubrication—Check the oil level at both ends of the blower daily. The oil change period is typically governed by operating conditions, such as load, temperature, dirt, humidity, fumes and the quality of oil used. This is typically stated in the user manual. Good practice is to change the oil often enough that it appears clean and clear when drained from the sump. The oil sump should be periodically flushed with a clean solvent. Proper filling using the factory recommended oil and maintaining to recommended levels is important to properly lubricate the blower. Always use clean containers for oil and cleaning solvents. Utilizing an oil analysis program can also be advantageous.
Air Filters & Filter Silencers—Servicing frequency of filter elements is not time predictable. A di!erential pressure indicator, with a continuous gauge reading, should be installed across the inlet filter. It will tell how much of the service life of the filter element has been used. It will also eliminate both premature filter servicing and premature blower failure due to a plugged filter when the filter pressure drop is used to establish maintenance points. In all cases refer to the filter manufacturer’s service instructions.
Vibration Monitoring—Vibration is dependent on many factors including foundation construction, shaft alignment, piping configuration, drive type, and operating conditions. High vibration at commissioning may indicate an installation issue or system resonance. Increasing vibration levels over time typically indicate the onset of a failure mode. Periodic or continuous vibration readings can be used to detect problems early.
Browse Carotek's selection of Blowers.
Information courtesy of Gardner Denver