Featured Pump Articles
- Grundfos Pumps in Industrial Water Treatment
- Grundfos Pumps in Industrial Temperature Control
- Grundfos Pumps in Process Liquids Transfer
-
Grundfos Pumps For Industrial Machining
- Turkey Processing Plant Saves $50,000 and Reduces Energy by 50% with a High Pressure Washdown
- Save up to 50% Energy by Optimizing Pumps
- Grundfos Food & Beverage Process Water Case Studies and Product Features
- AODD Pumps and Diaphragms for Food & Beverage Applications
- Are You Using Counterfeit Pirated AODD Pump Parts ?
- Industrial Blower Service Maintenance Guide
- Wilden AODD Pumps Outperform ARO, Yamada, Graco, Sandpiper, Versamatic and Murzan
- Centrifugal Pump Training in Minutes by Griswold
- Market Proven! Ethanol Extraction Pumps
- Carotek solves customer's leaky seal and pump cavitation problem
- Gear Pump Troubleshooting Checklist and Videos
- Case Study: Plant Solved Shaft Breaks in Positive Displacement Gear Pumps?
- Request a FREE Pump Site Survey ($2500 value)
- How To Set Up a Pump Reliability Program - Do You Know When Your Pumps Will Fail Next?
- Tips to Improve Your Pump Uptime
Grundfos Pumps For Industrial Machining
Many of Grundfos pumps are very well suited for industrial machining processes such as the End Suction, Inline Multistage and Immersible pumps. Choosing the right pump for the application will ensure the pump can handle the stress of machining operations.
Pump Challenges in Machining
Pumps are widely used throughout industry in machining. In general, pumps have three functions in a machine center:
- to cool the process
- to lubricate the tools
- to bring the liquid to the filter and back
These processes are an integral part of maintaining fast production and prolonging tool life. In addition, they must be done with energy efficiency and at the lowest possible total cost.
Among the challenges machining pumps typically face is the frequency of start/stop cycles. These cycles from zero pressure to max pressure cause huge stress on both pump and motor. Therefore, pumps for machine tool operations must be designed more robustly than, for example, standard water pumps. The motor can also be stressed if it doesn’t get sufficient cooling, which may happen when it doesn’t operate long enough for the cooling fan to become effective.
Another common pump problem in machining is that the shaft seal wears out quickly because the liquid pumped often contains small particles. When the shaft seal wears out it starts to leak more and liquid runs or sprays out onto the top of the tank.
Some machining processes are particularly sensitive, and any form of downtime means these processes become incomplete. Even if an issue arises from a relatively small component within a complex machinery system, such as a pump, financial losses can add up.
Grundfos Pumps for Machining
Robust, reliable Grundfos pumps are designed to offer pump speed precision and control – essential elements for machine tool coolant pumps and high-pressure pumps. In addition, pumps can be optimized to allow over synchronous operation for further flexibility.
Some of the Grundfos pump types most commonly used in machining are end suction pumps, inline multistage pumps, and immersible pumps. Integrating the pump system with controls and monitoring further enhances performance and efficiency of industrial machining processes.
Grundfos pumps cover an extensive range of performance options and variations for machining applications:
- all flow and pressure types
- 1 to 100 m³/h flows
- heads from 5 m to 100 bar
- modularization, customization
- various material options
- immersed depths ranging from 130 to 1500 mm
Grundfos End Suction Pumps for Machining
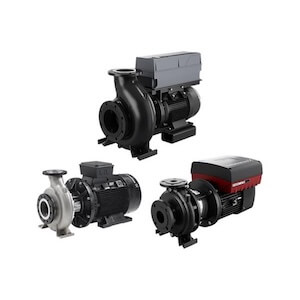
Grundfos end-suction pumps are an optimal solution for industrial processes that involve machine tools. Because machine tool pumps are used for circulating and recycling lubricating coolants, Grundfos end suction pumps are designed to provide exceptional accuracy and stability. Those attributes support delicate machining processes such as boring, turning, spark erosion, milling, sawing and wire cutting.
More Information
Grundfos Inline Multistage Pumps for Machining
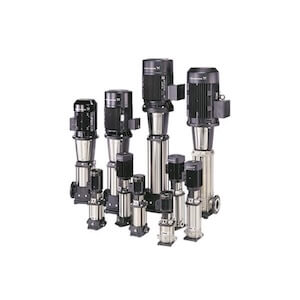
Grundfos end-suction pumps are an optimal solution for industrial processes that involve machine tools. Because machine tool pumps are used for circulating and recycling lubricating coolants, Grundfos end suction pumps are designed to provide exceptional accuracy and stability. Those attributes support delicate machining processes such as boring, turning, spark erosion, milling, sawing and wire cutting.
More Information
Grundfos Immersible Pumps for Machining
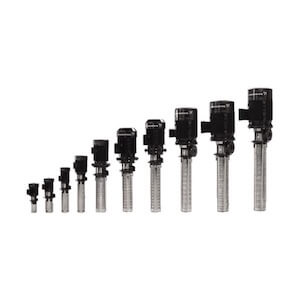
In machining, Grundfos immersible pumps are primarily used to efficiently remove coolant and cutting fluids from the machining process. Especially in situations where large volumes of liquid containing metal chips and debris need to be pumped away from the work area, immersible pumps allow for continuous operation and prevent contamination of the machine and surrounding environment. Immersible pumps can handle abrasive particles and can be submerged directly into coolant tanks.
Grundfos intelligent e-pumping solutions are designed to provide consistent, optimized flow and pressure for machining processes. For example, compact MTRE immersible e-pumps adapt to various high-pressure machining demands. With built-in frequency drive motors, intelligent sensors, and BUS communication capabilities, MTRE pumps ensure precise machining system monitoring and control for cost-effective, energy-efficient processes and minimal downtime.
Grundfos MTA single‐stage immersible pumps are designed especially for filtering systems in the machine tool industry. Semi‐open impellers allow the passing of chips up to 10 mm, making these compact pumps ideal for removing liquid from any machining process – from boring and milling to grinding. MTA pumps can efficiently transport liquid containing chips, abrasive particles and fibers on to the filtering unit.
More Information
Grundfos Machining Pump Distributor
A durable, reliable machining pump ensures that nothing interferes with your machining processes. As a factory-trained stocking distributor of Grundfos pumps, Carotek can help you harness the power of Grundfos advanced machine tool and industrial system cooling solutions